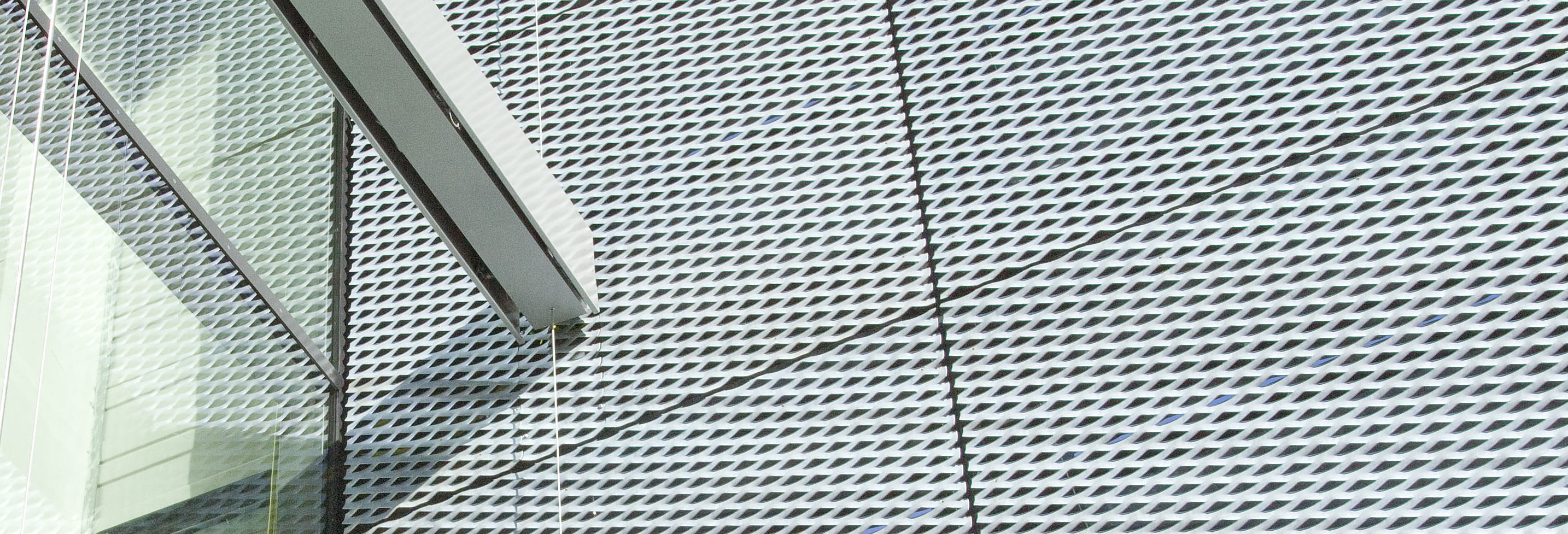
VORSICHT SALZSPRÜHNEBEL-TEST!
Ergebnisse sind nicht übertragbar auf die Praxis
Wer im Bau-, Produktions- oder Engineering-Bereich schützende Oberflächen einsetzt, sollte sich mit einem Aspekt des Korrosionsschutzes genauer befassen: der Bedeutung und den Grenzen von Kurzzeit-Korrosionstests im Labor. Seit Jahrzehnten sorgt der sogenannte „Salzsprühnebeltest“ für Missverständnisse im Hinblick auf die Leistung von Korrosionsschutzsystemen. Seine Ergebnisse werden werblich immer wieder als Leistungsindikator angeführt, obwohl bekannt ist, dass die Ergebnisse in Kurzzeittests besser ausfallen als unter realen Praxisbedingungen.
Was ist also falsch am Salzsprühnebeltest?
Der Test spielt in erster Linie in der Qualitätskontrolle bestimmter Materialien oder Beschichtungen eine Rolle. Das ist der ursprüngliche Zweck, zu dem der Test entwickelt wurde und zu dem er in einigen wenigen Branchen nach wie vor erfolgreich eingesetzt wird. In den meisten Branchen findet der Salz-Sprühnebeltest jedoch keine Verwendung mehr, selbst die Automobilindustrie verzichtet mittlerweile darauf.
Das Problem ist, dass der Salzsprühnebeltest regelmäßig eingesetzt wird, um Materialien oder Beschichtungen zu vergleichen oder zu klassifizieren, die völlig unterschiedliche Eigenschaften haben. Besonders irreführend ist die Verwendung des Tests für den Vergleich von Farb- und Metallbeschichtungen. Ähnlich wenig aussagekräftig sind Vergleiche verschiedener Metallüberzüge anhand dieses Tests. Er bringt z. B. bei Vergleichen zwischen Zink- und Zinklegierungsüberzügen, d.h. von Legierungen mit geringen Magnesium- und Aluminiumzusätzen, Ergebnisse zutage, die von der tatsächlichen Leistung unter Realbedingungen erheblich abweichen.
Leider werden solche Materialvergleiche noch immer anhand des Salzsprühnebeltests durchgeführt, obwohl es in der zugehörigen internationalen Norm DIN EN ISO 9227 ausdrücklich heißt: „Nur selten besteht ein direkter Zusammenhang zwischen der Beständigkeit gegen die Einwirkung von Salzsprühnebel und der Beständigkeit gegen Korrosion in anderen Medien. Die verschiedenen Faktoren, welche das Fortschreiten der Korrosion beeinflussen, können sich je nach den herrschenden Bedingungen sehr unterschiedlich auswirken. Dazu gehört z. B. auch die Bildung von Schutzschichten. Die Prüfergebnisse sollten deshalb nicht als direkter Hinweis auf die Korrosionsbeständigkeit der geprüften metallischen Werkstoffe in allen Umgebungsbedingungen betrachtet werden, in denen diese Werkstoffe verwendet werden können.“ [1]
Zudem weist die Norm darauf hin, dass der Test sich lediglich zur Qualitätskontrolle eignet. Viele von Experten geprüfte Fachartikel warnen ausdrücklich vor der Anwendung des Salzsprühnebeltests. Hier einige Beispiele:
„Schon seit einigen Jahren ist allgemein anerkannt, dass bei der Leistungsbewertung organischer Beschichtungssysteme die Ergebnisse des standardmäßigen Salzsprühnebeltests und die tatsächliche Korrosionsbeständigkeit in der Praxis – wenn überhaupt – nur selten übereinstimmen.“ [2]
„Der Salzsprühnebeltest ist der am häufigsten eingesetzte Test zur beschleunigten Korrosionsprüfung. Er wurde vor über 50 Jahren zur Überprüfung des Korrosionsverhaltens von Metallbeschichtungen in maritimer Umgebung entwickelt. Obwohl sich vielfach gezeigt hat, dass dieser Test keinen zuverlässigen Hinweis auf die Korrosionsbeständigkeit von Beschichtungen im Außenbereich gibt (nicht einmal in salzhaltiger Atmosphäre), hat er sich in der Beschichtungsindustrie fest eingebürgert“. [3]
„Der weitläufig bekannte Salzsprühnebeltest ASTM B-117 vergleicht kaltgewalzten und feuerverzinkten Stahl und liefert innerhalb weniger Stunden Ergebnisse. Leider schafft es der Test nicht, die bewiesenermaßen höhere Korrosionsbeständigkeit der feuerverzinkten Probe gegenüber der nicht verzinkten Probe nachzuweisen.“ [4]
„Das Besprühen mit Salz sorgt für eine rasche Degradation der Oberfläche. Diese ist jedoch kaum mit der Verschlechterung der Materialeigenschaften unter realen Bedingungen vergleichbar. Die durch Salz angestoßene Degradation folgt anderen Mechanismen als die Degradation unter realen Außenbedingungen. Daher liefert der Test relativ unpräzise Ergebnisse.“ [3]
Leider wird der Salzsprühnebeltest trotz aller Gegenargumente nach wie vor in der Vermarktung neuer Beschichtungen und Materialien als Qualitätsindikator angeführt.
Warum liefert der Salzsprühnebeltest irreführende Ergebnisse?
Um zu verstehen warum der Salzsprühnebeltest die tatsächliche Korrosionsbeständigkeit eines Materials nicht zuverlässig voraussagen kann, muss man den Testvorgang genauer betrachten. Proben werden in eine temperierbare Kammer gegeben und bei 35° C mit einer salzhaltigen Lösung besprüht. Da das Aufsprühen durchgängig erfolgt, sind die Proben die ganze Zeit über feucht und damit Korrosionskräften ausgesetzt. Die Korrosionsbeständigkeit wird anhand der Menge des auftretenden Oberflächenrosts bestimmt. Die Testdauer liegt zwischen 24 und 1000 oder mehr Stunden.
Der Salzsprühnebeltest kann jedoch aus mehreren Gründen keine realen Korrosionsbedingungen schaffen:
- Die Oberfläche der Proben ist konstant feucht, trocknet zwischendurch nicht ab. Allein das entspricht nicht den realen Bedingungen. Metalle wie z. B. Zink können so im Test keine passive Schutzschicht bilden, wie sie es unter realen Bedingungen tun.
- Der Chloridgehalt im Sprühnebel ist sehr hoch (in der Regel 5 % NaCl), was dazu führt, dass die Korrosion stark beschleunigt wird. Allerdings sind unterschiedliche Metalle und Metallbestandteile unterschiedlich anfällig für verschiedene Beschleunigungsfaktoren.
Die im Test erzeugten Umgebungsbedingungen sind nicht realistisch und härter, als es beim normalen Einsatz im Außenbereich der Fall ist.
Der Salzsprühnebeltest eignet sich nicht für den Vergleich der Korrosionsbeständigkeit verschiedener Materialien
Mittlerweise ist erwiesen, dass die in der Praxis beobachtete gute Korrosionsschutzleistung von metallischen Zinkbeschichtungen auf das Abtrocknen zwischen den Nassphasen zurückzuführen ist. Durch die Entwicklung einer passiven und relativ stabilen Oxid- und/oder Carbonatschicht während der Trockenphase werden feuerverzinkte Oberflächen besonders korrosionsbeständig. Die ununterbrochen feuchten Bedingungen während des Salzsprühnebeltests verhindern, dass sich eine solche passive Oxid-/Carbonatschicht bilden kann. Beim Salzsprühnebeltest wird zudem der schädigende Einfluss von UV-Licht auf lackierte Oberflächen komplett außer Acht gelassen. Das ist ungünstig, weil damit die wichtigste Ursache für die Verschlechterung lackierter Stahlteile überhaupt nicht berücksichtigt wird.
Beim Vergleich verschiedener Zinküberzüge liefert der Salzsprühnebeltest ähnlich verzerrte Ergebnisse. So führt die Zugabe kleiner Mengen von Magnesium oder Aluminium zu einer Zinklegierung im Test zu Ergebnissen, die stark von der Realität abweichen. Magnesiumionen, die entweder aus der Umgebungsatmosphäre stammen (Meersalz) oder in einer Zinklegierung beigemischt werden, fördern bei Exposition gegenüber Natriumchlorid die Bildung korrosionshemmender Stoffe und senken damit den Korrosionsgrad. Das erklärt, warum Beschichtungen aus Zink, Magnesium und Aluminium unter Testbedingungen bei kontinuierlicher Exposition gegenüber Feuchtigkeit und hohen Natriummengen bessere Ergebnisse erzielen als reine Zinkbeschichtungen. Dieser Effekt ist auch bei Tests unter realen Bedingungen zu beobachten, z. B. in maritimer Umgebung. Allerdings fällt die Abweichung hier wesentlich geringer aus als beim Salzsprühnebeltest.
Fazit
Die Verwendung des Salzsprühnebeltests zur Bewertung der Leistungsfähigkeit von Beschichtungen und Metallüberzügen für Stahlteile bleibt weiterhin ein großes Problem. Obwohl Korrosionsschutzexperten die Grenzen des Tests genau kennen, wird er immer noch als Verkaufsargument für Korrosionsschutzsysteme angeführt, die im Test besser abschneiden. Wir hoffen, dass dieser Artikel einen kleinen Einblick in die
wissenschaftlichen Hintergründe gibt, die die Grenzen derartiger Kurzzeittest im Labor aufzeigen. Wenngleich schnelle und kurzfristige Ergebnisse auf den ersten Blick verlockend erscheinen, sind Ergebnisse aus Langzeittests und praktische Erfahrungen mit echten Konstruktionen unentbehrlich.
Autoren:
Lena Sjögren, Koordinatorin - Consulting-Services und Korrosion Swerea KIMAB AB
Murray Cook, Geschäftsführer der European General Galvanizers Association
Swerea KIMAB
Swerea KIMAB ist ein führendes Forschungsinstitut im Bereich Korrosion und Materialkunde mit Sitz in Stockholm. Seine Spezial-gebiete sind Oberflächentechnologie, Korrosion und Korrosionsschutz von Metallen, Korrosionsschnelltests, Praxistests, Korrosion von Polymeren, Materialanalyse und Metallografie.
Quellen:
[1] DIN EN ISO 9227 ‘Korrosionsprüfungen
in künstlichen Atmosphären – Salzsprühnebelprüfungen’.
[2] Skerry, J S, Alavi, A and Lindgren, K I. ‘Environmental and Electrochemical Test Methods for the Evaluation of Protective Organic Coatings’, J of Coatings Technology, vol 60, No 765, p97.1988.
[3] Appleman, B. ‘Cyclic Accelerated Testing: The Prospects for Improved Coating Performance Evaluation’, J Protective Coatings & Linings, p71-79. Nov 1989.
[4] Townsend, H E. ‘Development of an Improved Laboratory Corrosion Test by the Automotive and Steel Industries’, Proceedings of the 4th Annual ESD Advanced Coating Conference, Dearborn, USA, 1994.